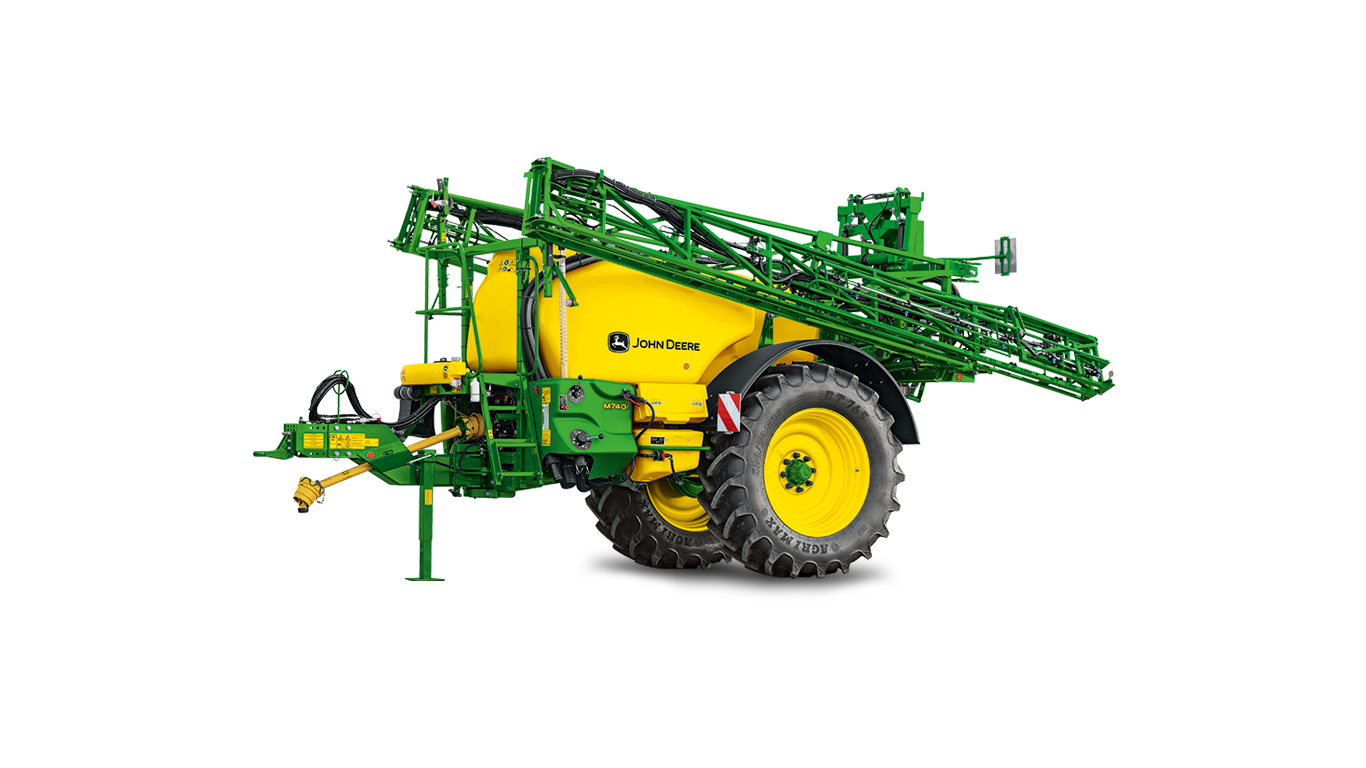
M724i
Trailed Sprayer
- 2,400 L tank volume
- 400 L rinse tank
- 280 L/min pump capacity
- Sprayer control with multi functional lever (joystick)
Features
Simply ideal, multiple solutions to level up spray performance
The M700i Series Trailed Sprayers will make crop protection simply ideal. A broad configuration possibility offers multiple solutions to level up spray performance where needed, in order to meet various value chain requirements. Smart solutions make spraying more productive and cost efficient, without compromising on the uptime.
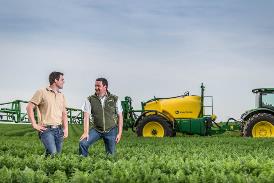
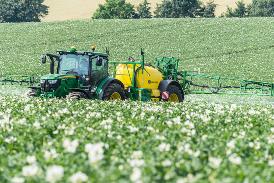
The M700i Sprayers offer the right answer for many crop care process needs. A wide range of configuration possibilities is available to match various value chain requirements. Investments can be made where they are needed the most. To keep crop protection input cost under control, all M700 Series Sprayers are prepared for automatic section control.
When it comes to uptime, the M700i Series are designed based on the same insights as the successful John Deere 700 Series platform, using similar proven components to meet quality and reliability levels that are expected from a trailed sprayer combined with a higher level of intelligent solutions. From filling up to spraying and rinsing, the ergonomic layout of the operator’s station with manual valves will command the liquid into the right direction.
The round-shaped polyethylene tank is fully cradled by the frame and gives the machine a low center of gravity; this comes together with the z-bar parallelogram and double-linked axle suspension, providing stability needed on the road and in the field without losing valuable time. The 2400-L (634-gal.), 3200-L (845-gal.) or 4000-L (1057-gal.) tank sizes combined with the full-range durable steel spray booms from 18 m (59 ft) up to 30 m (98 ft)* allows the operator to cover the field quickly and accurately.
The operator is in control with in-cab operation, which is set up to have all the functions within arm’s length. All machines come with a multi-functional lever for fast and easy operation.
- M700i ISOBUS-ready
- Ease of operation: logic and ergonomic manual operator’s station
- Functionality or comfort: three levels* of hydraulic operation, selective control valve (SCV), hydraulic selector or full electrohydraulic control with or without load sense
- Standard equipped with multi-functional lever for sprayer operation
- Display options including 4240 Universal Display, or 4640 Universal Display to suit producer needs
*NOTE: Check Build & Price for possible configuration combinations.
Proven components from successful 700 platform offer uptime on M700i
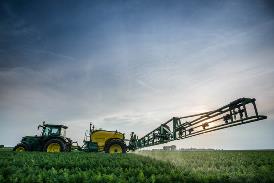

The M700 Series is designed with the same insights as the successful 700 Series, using proven components to maximize uptime and performance, while electronic solutions have been added to support easier operation and cut back on operational costs.
- Durable round-shaped polyethylene tanks 2400 L (634 gal.), 3200 L (845 gal.), and 4000 L (1057 gal.)
- 400-L (106-gal.) rinse water tank
- Self-priming piston diaphragm pump 280 L/min (74 gpm) with 5.1-cm (2-in.) filling connection
- 55-L (14.5 gal.) chemical inductor hopper
- Layout of operator’s station for easy to control and easy access to filters and connections
- Durable mainframe cradles the tank and boom lift system
- Optional double-linked, axle suspension, maintenance-free polyurethane dampers
- Fully welded 10-bolt rims for wheels and tires
- Spray booms are cradled during transport in the rolls, minimizes bouncing, providing uptime
- Slim design, durable fixed or steering drawbar for accurate tracking
- Durable steel spray booms including Z-bar parallelogram boom lift system
Low-line design offers performance and uptime in the field and on the road
The round-shaped polyethylene tank is fully cradled by the frame and gives the machine a low center of gravity. This comes together with the double-linked axle suspension, providing stability needed on the road and in the field.
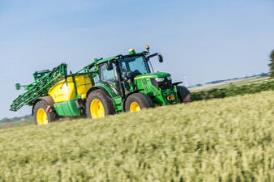
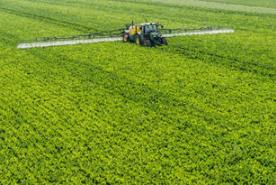
With its low center of gravity and even weight distribution, the M700i Series are built for stability. The entire chassis designed especially for the job and the Z-bar parallelogram boom lift system connects directly to the chassis to keep the center of gravity low. The frame cradles the large, durable polyethylene tank perfectly. The special tank shape limits chemical residues and always provides exceptional stability.
Spray booms being held firmly but gently in transport position using the rolls at the front allow vertical movement and prevent wear and tear to the boom.
The optional double-linked axle suspension offers uptime, comfort, and performance on the road and in the field. The frame, tank, and single-axle design offer better maneuverability. Regardless of the boom position, the level weight distribution helps to keep the machine steady.
Due to the special tank design, additional tank baffles are not required. It is easier to agitate liquid due to the smooth tank that has less risk of spray solution sticking to the inside of the tank.
- Low-line design offers stability in the field and on road
- Z-bar parallelogram boom height adjustment is a unique John Deere feature
- Tank with lower center point of gravity supports stability
- Slim drawbar design offers better maneuverability
- Round-shape polyethylene tank for perfect agitation; smooth tank surface for easier rinsing inside and outside
- Deep sump for better emptying, even on hillsides
- No baffles or dead corners supports better solution mixing
- Perfect readout, digital tank level indication (option)
- Dry liquid level indication comes standard
Z bar-parallelogram boom lift system lowers the center of gravity
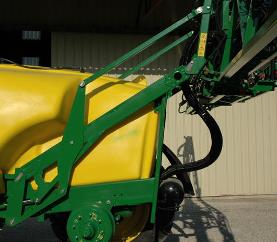
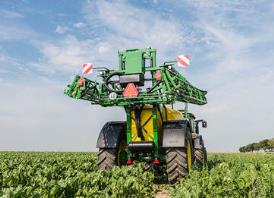
The specially designed Z-bar parallelogram offers ground clearance at the rear; hydraulics lift the boom gently and smoothly. Because the boom lift cylinders are located on either side of the chassis, it offers a low center point of gravity without compromising on stability.
- Equal boom lift adjustment
- Maximum ground clearance at the rear
- Accumulator suspends vertical boom movement in spray mode
- Minimize bouncing in transport mode, boom being held firmly and gently at transport rolls
Operator’s station layout delivers easy control
Ergonomic operator’s station design makes operation fast and easy. All levers are grouped together and with the large handles, set up is performed quickly. The operator’s station is available in manual control with additional automation when it comes to agitation or dilution.
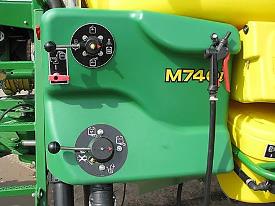
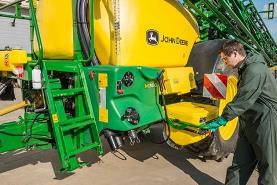
The ergonomic design of the operator’s station makes operation easy and convenient. The large handles limit the risk of mistakes and save valuable time by efficiently setting up the machine.
The easy-to-set manual valves speed up spraying operations and will make filling, spraying, and rinsing even faster, easier, and more accurate. Both main valves will point in the same direction within the main operation steps to limit mistakes during the operation.
The chemical inductor hopper, spray gun, and clothing lockers are partly stored behind the valve area. Filters and hose connections are easily accessible.
The wet solution system is designed with a primary circuit that supplies working pressure to agitation injectors, rotating rinsing nozzles, and a chemical inductor hopper. A second circuit with spray pressure regulator automatically sets spray pressure to the spray boom. This ensures the right pressure is there.
- Limiting risk of mistakes during operation, with easy-to-operate valve layout
- Dry level-indicator for accurate actual tank readout
- Easy access to filters and hose connectors
- Two-compartment clothing locker is optional
- Large, 55-L (14.5 gal.) inductor-hopper stored behind the valves (option)
- Self-priming piston diaphragm pump with 5.08-cm (2-in.) filling connection
- Standard recirculation valve allows better emptying and most efficient rinse-water usage when rinsing
- Filling point rinse-water tank near the operator station (no walkaround needed for refill)
- Parking positions for hydraulic hoses, electric cables, and connectors at front under the platform
Logical operator's station makes machine set up fast and easy
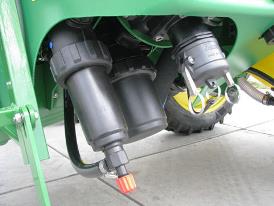
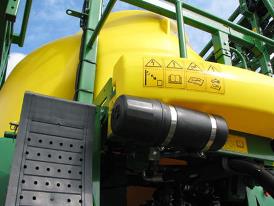
All the filters and connectors are grouped together for easy access. Filters can be cleaned even with full tank(s). A standard recirculation valve allows better emptying and most efficient rinse water use when cleaning the sprayer. The mandatory chemical safety card holder is located near the platform, making the product information readily available.
- 5.1 cm (2-in.) fill hose connection angled toward easier operator connection
- Transfer valve, 5.1-cm (2-in.) transfer liquid from main tank to external point
- 5.1 cm (2-in.) quick connector for filling rinse water tank (optional)
- Ecomatic chemical closed transfer system connection (optional)
- Side step easy access to tank lid
- Huge 400-L (10-gal.) rinse-water tank
- 5.1-cm (2-in.) filling hose with bracket located at platform (option)
Make filling easy; 55-L (14.5-gal.) chemical inductor hopper safely transfers chemicals into the tank
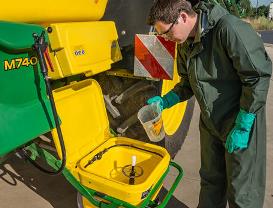
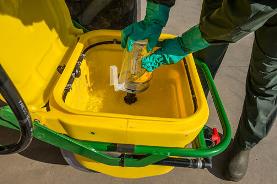
The optional 55-L (14.5-gal.) polyethylene chemical inductor hopper is located partly behind the valve cover, to minimize dirt from the wheels from entering on top of the inductor. The polyethylene hopper inside is smooth and supports easy cleaning. Filling the inductor with water is easy using a standard ring-line to supply water on demand into the inductor. Package cleaning is made safe simple and easy, as the rinsing head is based on a push-to-rinse system to provide a safe package cleaning when using both hands. The rinse head is off-center positioned, which allows better cleaning for odd-sized packages or larger containers. Transferring the prepared mix into the tank is done easily by opening the valve at the operator’s station with a powerful injector on top of the tank creating a vacuum at the inductor. In this way, liquid enters directly via the basket strainer in top of the tank, reducing the risk on foaming during filling.
Transferring inductor hopper content into the main tank is done using an injector. This prevents contamination at the supply line to the inductor hopper. Whenever using the sprayer pump for filling the sprayer with clean water, it is also delivered into the hopper.
- Inductor hopper with off-center rinsing head in inductor allows cleaning odd-sized packages
- Rotating rinse head optimizes cleaning and reaches package inside better
- Setting up is easy - primary pressure circuit supplies correct working pressure to the inductor
Keep crop protection costs under control - intelligent solutions cuts costs and boosts productivity
Keep costs under control with intelligent solutions that reduce input costs and enable increased productivity. Spray process set up, control, and monitoring appears on an optimum operator’s interface with the machine. Automatic section control, guidance, TerrainControl™ Pro and light-emitting diode (LED) work lights are solutions to optimize crop protection quality and extend the available spray window.
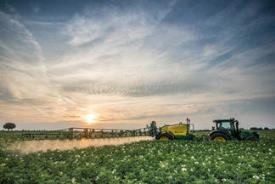
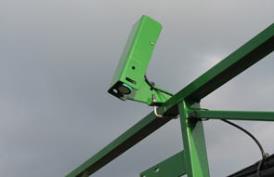
Integrated solutions on the M700i collectively cooperate to optimize crop protection. Automatic section control or SprayerPro will switch the sections automatically in predefined areas, saving valuable input cost. The M700i has the optional TerrainControl Pro system that adjusts boom tilt and boom height to optimize spray boom position in various field circumstances. Once the steering drawbar is available, the sprayer’s own headland management system (HMS) will automatically control the drawbar steering at the headland only when needed. Powerful LED lights provide the visibility to get the job done after dark.
- M700i TerrainControl Pro offers soil, crop, and hybrid modes, plus headland lift for added convenience
- Halogen or LED working lights available for night spraying
- Drawbar steering with HMS controls the drawbar when needed
Proven components from the M700i increase efficiency
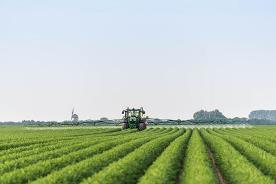
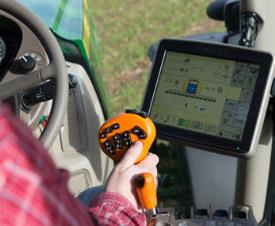
Intelligent sprayer solution controls feature premium precision and maximized uptime, smart solutions, and spray accuracy.
- The right nozzle selection, integrated nozzle calculator, and real-time droplet size indication in the display
- Actual indication speed, rate, pressure, flow, field data, distance, sections active or in active, boom tilt position machine data, and many more
- Automatic rate controller with automatic or manual spray rate adjustment with boost function
Multiple optional solutions on the M700i offer additional premium precision. Take care of all important machine functions with process information displayed in the comfort of the cab.
- Pressure and flow sensor at the sprayer provide the highest spray accuracy and real-time information
- Low-flow detection, rate control automation; once flow sensor measurement is out of range, pressure sensor takes command
- Crossflow check detects nozzle wear, spray line blockage or wrongly programmed nozzle sizes
- Anticipation factor supports concentrated start when switching manual sections at the headland
- Start delay pressure regulator prevents under dosage at spray start in field corners
- Default valve setting prevents overdose, controls spray pressure setting at spray start after refill
- Accuracy, digital tank level indication
Rinsing and dilution is fast and easy with AutoDilute
The M700(i) Trailed Sprayers will make crop protection simply ideal. A broad configuration possibility offers multiple solutions to level up spray performance where needed, in order to meet various value chain requirements. Smart solutions make spraying more productive and cost efficient, without compromising on the uptime.
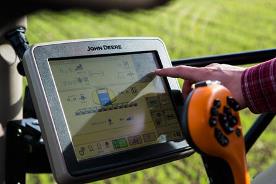
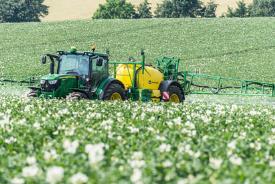
John Deere's award-winning multi-cycle dilution system for controlled residue disposal is an equipment option on the M700(i) Sprayers.
NOTE: Always refer to the chemical package and read the safety requirements when diluting or rinsing a sprayer.
AutoDilute enables operators to dilute the sprayer without leaving the cab. Operators save valuable time since there is no longer a need to walk to sprayed crop to reposition sprayer valves. The time savings from AutoDilute helps prepare the machine faster for the next application. AutoDilute meets the environmental legislation in countries where dilution of the remaining crop protection chemical in the machine is a legal requirement. (Please refer to local legal requirements.)
The AutoDilute integrated multi-cycle dilution system features:
- AutoDilute - easy to operate with lower risk of mistakes
- AutoDilute controlled dilution factor using automatic stepwise residue dilution
- Continuous dilution fast flush between jobs
- Continuous dilution can be combined with stepwise dilution first followed by continuous dilution
- Efficient rinse water usage, amount of rinse water can be programmed to the needs
- Optimum dilution - using automated steps, AutoDilute stepwise dilution is visible in each step
Fast dilution needed - select continuous dilution, AutoDilute stepwise dilution for controlled stepwise dilution for the best result. All steps are in the display while spraying the remaining liquid out of the tank.
*Check Price List for possible configuration combinations.
M724i