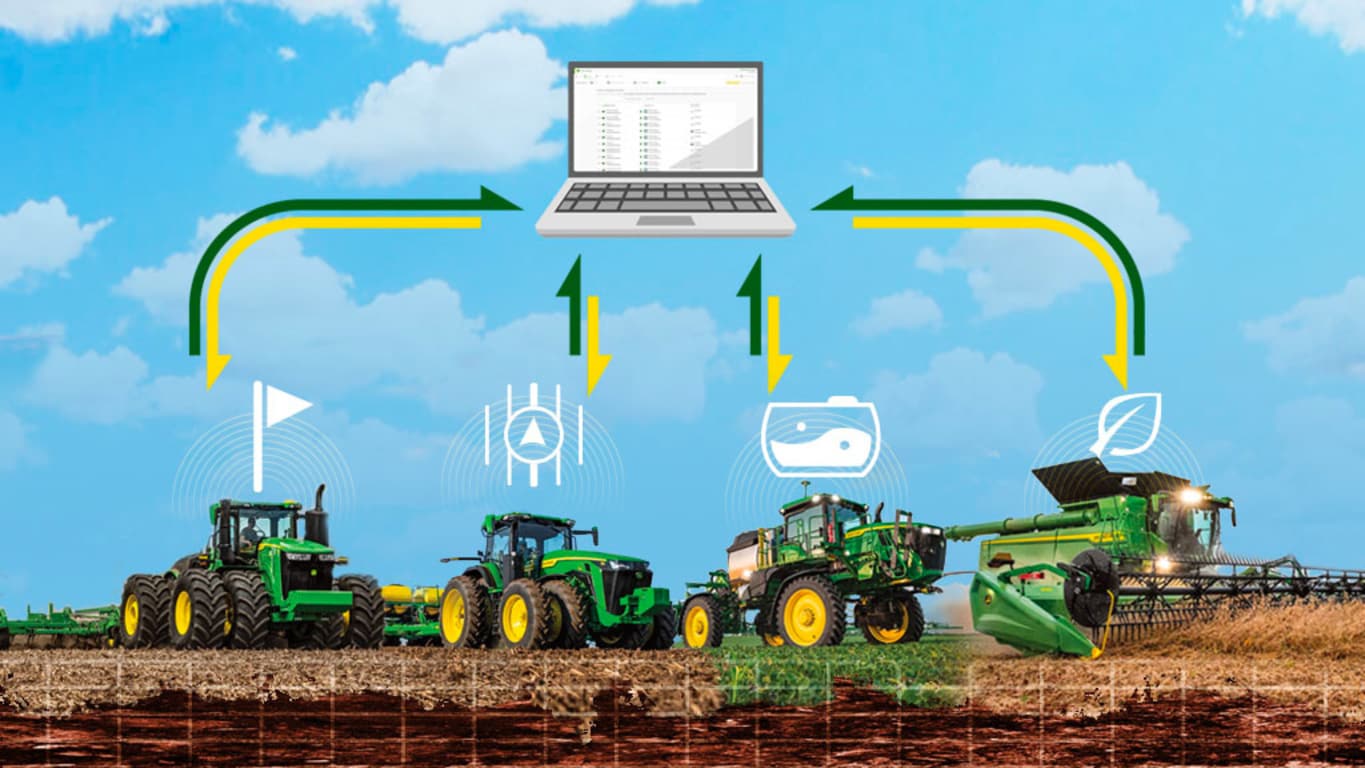
Data Sync Setup
- Save time – Auto-populate machines in-field with latest setup data
- Increase accuracy – Avoid manual entry errors and duplicates for better record retention and analysis
- Increase Efficiency – Seamlessly and automatically manage in-season changes throughout your entire connected operation
Features
Save time and get to the field faster with Data Sync Setup
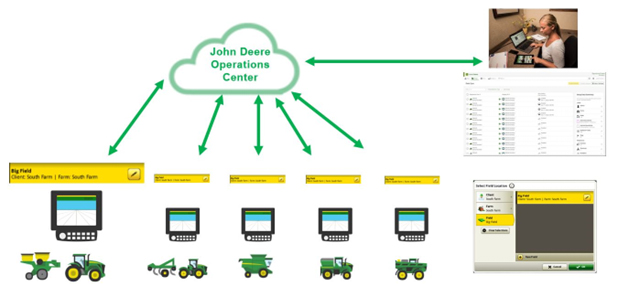
Save time and get to the field faster with Data Sync Setup
Data Sync eliminates time spent creating and transferring setup files between John Deere Operations Center™ and the latest John Deere Displays while consistently providing the right setup information where it’s needed, and at the right time. Data Sync Setup shifts your operation from a localized manual data management process to a shared centralized list that updates in near real time as data is created, modified, or removed.
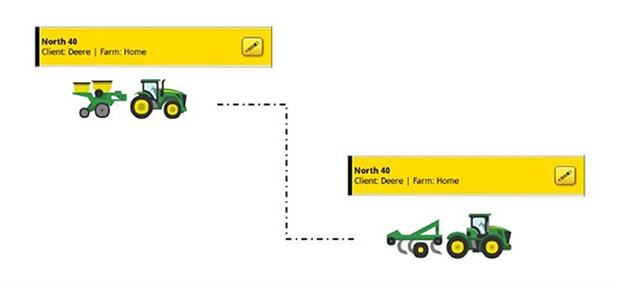
With Data Sync you can:
- Remove busy work associated to creating and sending setup files to machines
- Create, edit, or delete data in the field and automatically share those data management changes with machines operating within your sync’d organization
- Get to the field faster with automating what was before manual steps in managing setup data on and off machines
- Create guidance lines in one operation and automatically share them to a machine in a different operation: and with all enabled machines
Data available for sharing:
- Client/Farm/Field
- Boundaries
- Guidance Tracks (Straight, Curve, Circle)
- Products
- Tank Mixes
- Flags
- Variety Locator
- Operators
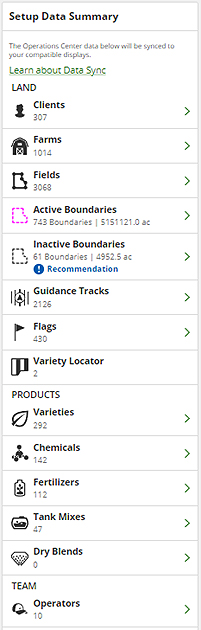
Improve data accuracy and efficiency through Data Sync Setup
Avoid manual entry errors
Syncing active setup assets in John Deere Operations Center™ to machines removes the manual entry of duplicates and incorrect entries that can occur with ongoing data management activities throughout the season. By leveraging one common data list, the work data will be available with the intended recorded field for accurate analysis and remote management. Having an accurate field, product, tank mix, and operator drives the intended results in Operations Center Field Analyzer and Analysis.

Less chance of duplication and less chance of spelling errors. By automating the steps with creating setup files, and working from one setup list, a farming operation can improve their ability to enter data correctly in the field.
Improve efficiency and reduce steps by syncing guidance lines
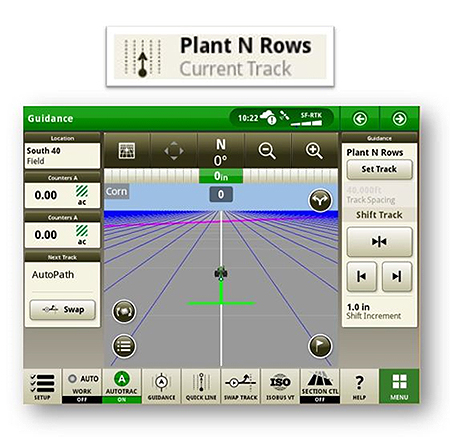
Guidance lines created in one operation are often needed by the next in a short time window. Data Sync removes manual steps with sending guidance lines and simply syncs with enabled displays and machines. Gain access to straight tracks, circle tracks, and AB curve tracks in the drop-down track list when spraying or side dressing in near real time after the planter has created the guidance line.
Share on-the-go changes
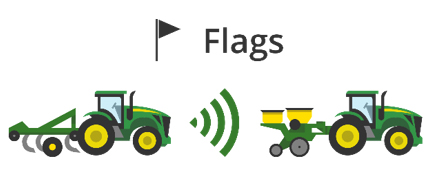
Map field events using flags to identify areas of avoidance. Note additional field work needed such as damaged tile lines or pre-season cleanup and share it with other connected machines within seconds. See flags on the coverage or as-applied map in machines joining the field later, created by a connected machine who marked it in an earlier pass.
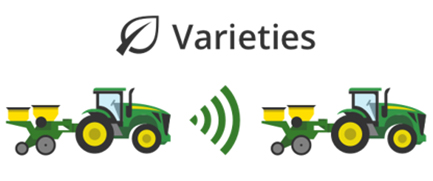
Add a variety in season that may have not been planned or made available in the beginning of the season. Add it with confidence knowing the other planting tractor will also have that variety in their drop-down list for use, and available for accurate data recording.
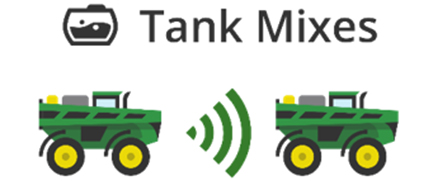
Make product or tank mix adjustments on the fly and get those changes as an updated selection entity on all sync’d machines. One shared setup list available for all within a connected organization and reflected in Operations Center.
Access the right data on the right machines at the right time
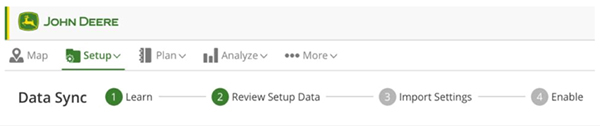
Data Sync can easily be turned on to start syncing to machines from John Deere Operations Center™ in the Setup tab. Review data that is set to be sync’d from Operations Center to the machines, ensure import settings are toggled correctly, and enable machines one by one to start syncing.
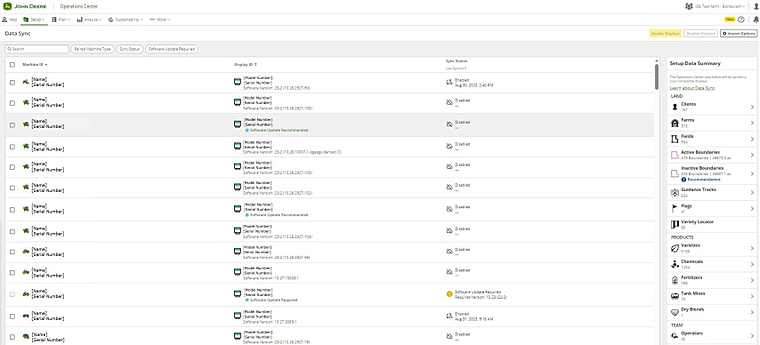
Enable connected machines to sync with Setup Data Summary shown on the right for a transparent operational overview. Number of data entities are listed to help with understanding of how many of each type will sync. Easily make corrections to setup data summary by clicking on entity type and linking to Land or Products where changes can be made.
Sync setup data, field data, and guidance lines to machines from Operations Center. Make changes on the go, and have those changes reflected in all machines’ setup data drop down lists.
Make changes from the cab and share with confidence
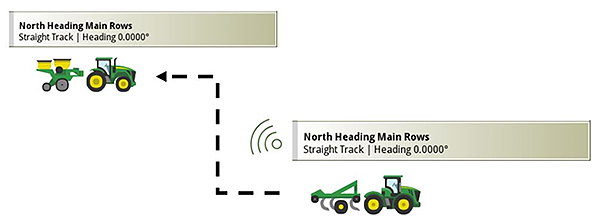
Data creations, edits, and removals can be shared with other connected machines within seconds. Share a new boundary, guidance track, or flag automatically without any extra button clicks.
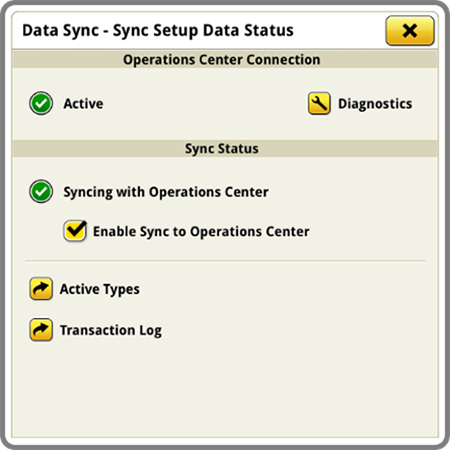
Work long days in the field with confidence that all machines are operating from one setup data list. The Status Center provides quick confirmation that your data is syncing. Within File Manager additional details outline last sync time and when individual entity types were received.
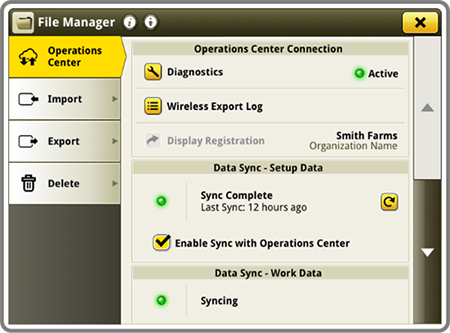
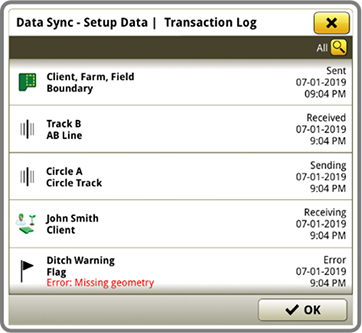
Flexible data management options
Not every operation has total operator trust to have complete control of one centralized setup data list. Both Operations Center and Gen 4/G5 Displays feature operator mistake proofing settings to provide more stability to the sync’d data list and prevent unwanted changes from happening.
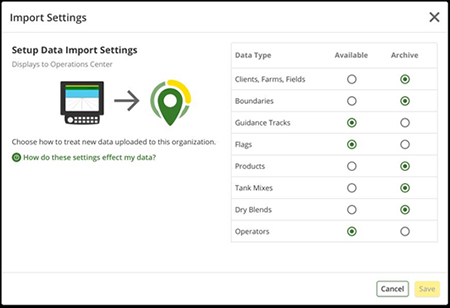
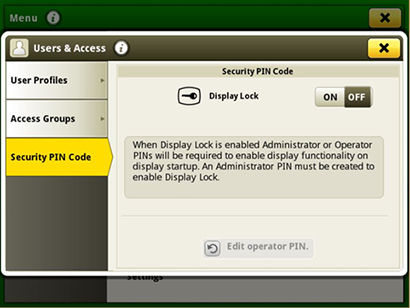
Automatically sync work data to John Deere Operations Center™
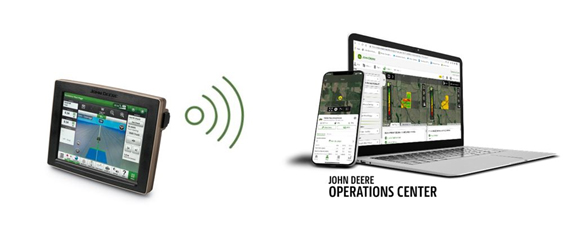
Gen 4 and G5 Displays send work data from the display to Operations Center every 30 seconds eliminating the need for manually exporting data. By taking out the manual step, users can work in the field with confidence their data is automatically sent and available in Operations Center. Work data is then processed for analysis use and made available in both web and mobile platforms. Sending work data automatically is made available with a JDLink™ connection and an established Operations Center organization. Sending work data automatically with Data Sync can be triggered on within the display.