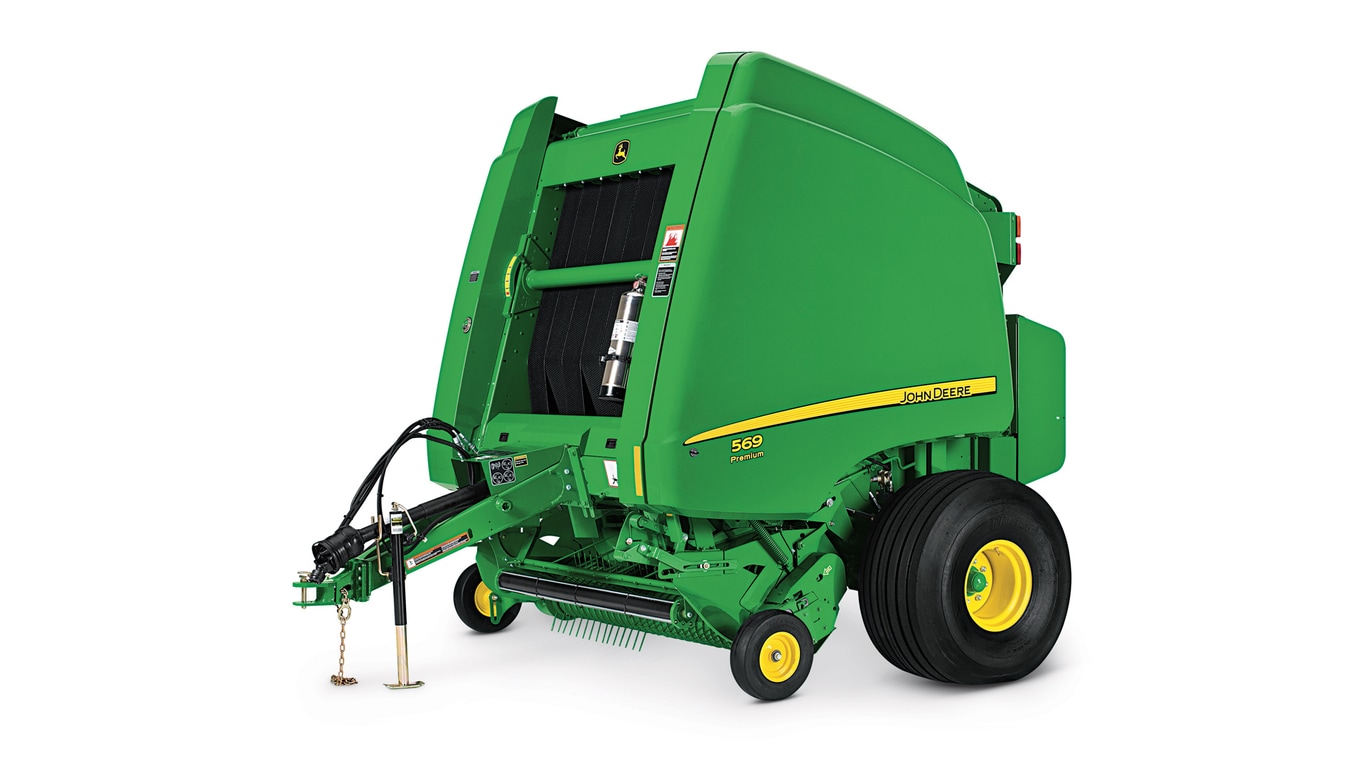
569 Premium
Round Baler
- ISOBUS monitor
- MegaWide™ Plus pickups
- Exclusive DiamondTough™ belts with plate-type splices
- Driven by Diamond® Chain for superior performance
Features
ISOBUS monitor replaces BaleTrak™ Pro monitor on premium machines
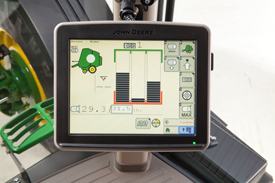

The John Deere 469 Premium and 569 Premium Round Balers are ISOBUS compatible. Premium machines require an ISOBUS display. BaleTrak Pro monitor will not work to run these Premium Round Balers.
This means the controller is now a part of the baler and the operator can use an ISOBUS-compatible display inside the cab. The ISOBUS system for premium round balers is compatible with John Deere 1800, 2600, and 2630 Displays for greater commonality and functionality. It can also be incorporated into the CommandCenter™ on R Series Tractors, as long as the tractor is ordered ISO ready (GreenStar-ready wiring harness option code 8064 or GreenStar AutoTrac™-ready wiring harness option code 8067on 6R Tractors).
If a tractor is not ISOBUS-compatible, a wiring harness can be ordered to make the tractor run the John Deere 469 and 569 Premium Round Balers. Wiring harnesses are available to order with the baler or can be ordered after the fact through Parts. Two wiring harnesses are necessary; the cab wiring harness and the battery wiring harness.
For customers with John Deere 30, 40, 50, 55, 60, or 70 Series Tractors or any competitive tractor, a specific harness is available that includes a zener diode to regulate voltage. For customers with 6000 – 8000 Series Tractors, the wiring harness needed does not include the zener diode, since regulating voltage should not be an issue. These harnesses are only used for baling applications and are not intended to work in other ISO implement applications that require the use of radar and GPS capabilities.
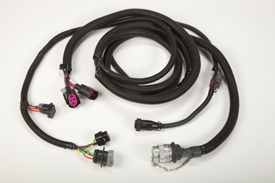

The ISOBUS system includes all of the great functions from the BaleTrak Pro monitor-controller, along with several new features as well.
Features of ISOBUS-compatible balers:
- Simple integrated technology reduces the need for an extra monitor
- Factory settings are preprogrammed but can be changed by the operator, if desired
- Touchscreen interface on 2600 and 2630 Displays allows for easier screen navigation and settings adjustments
- Bale size and certain twine settings can be adjusted from the operator’s seat
- One hundred separate field bale counters instead of one with BaleTrak Pro (10 customers and 10 fields per customer)
- ISOBUS displays can be interchanged with different ISOBUS-compatible balers and implements
- A more intuitive error code system with text instead of using error codes
- Easier operator interface navigation with descriptions when hovering over icons
- Common calibrations, except twine-arms, can now be made from the cab with no channels to work through
- Third bale shape sensor is standard on premium machines
- Third bale shape sensor can be turned on or off
- Maximum bale size button for finishing up fields
- Allows the operator to go to maximum bale size for last bale in field. Monitor will return to preset size after the bale is completed, wrapped and ejected.
- All premium machines are automation ready (please see Tractor-baler automation information for more details)
Adjustable hitch to match wide array of tractor drawbar heights
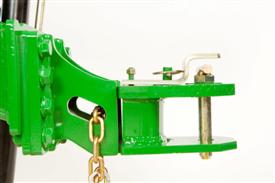
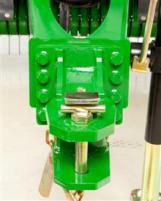
The 9 Series Round Balers come standard with an adjustable hitch. This feature allows the hitch height to be adjusted to optimize crop-feeding performance. Due to the wide array of tractor tire sizes and drawbar heights, hitch adjustment may be necessary to get the proper feed opening of the baler. The adjustable hitch eliminates the need for the 51-mm (2-in.) thick tractor drawbar kit (AE57344) because it has a wider opening.
Benefits of the adjustable hitch:
- Ability to match baler to numerous tire sizes
- Allows for drawbar height to fall within 330 mm to 559 mm (13 in. to 22 in.) from top of drawbar to the ground
- Eliminates narrow feed opening on baler which can cause plugging
- Allows pickup head to follow terrain without missing crop
All eight bolts must be used when adjusting the hitch. There are four different positions as shown below:
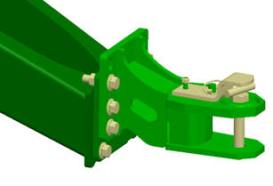
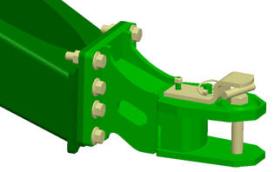
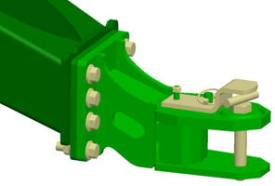
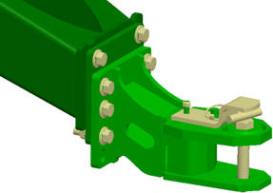
Also standard on all 9 Series Round Balers except the 459E is the drawbar flap. This helps to eliminate hay from getting caught on the hitch of the baler. The drawbar flap is designed to allow the operator to remove or attach the flap without having to unhook the baler from the tractor.
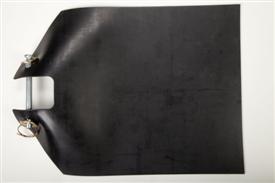
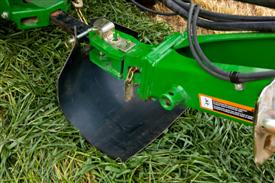
MegaWide™ Plus pickups on premium balers for heavy-duty operations
Available on the 569 Premium and 469 Premium Balers only, John Deere exclusive Premium MegaWide Plus pickup has been upgraded to offer larger components to meet those extreme demands. Premium MegaWide Plus pickups also come standard with hydraulic pickup lift to help customers be more productive when having to raise the pickup for transportation.
Changes to the Premium MegaWide Plus pickup include:
Larger cams and cam bearings
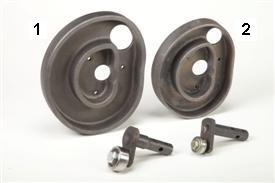

Larger spider gears for 1.22-m (4-ft) and 1.52-m (5-ft) pickups
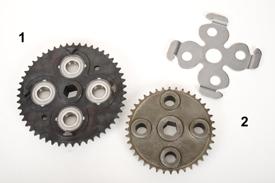
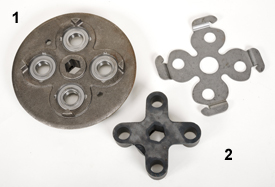
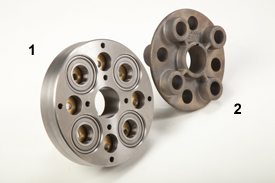

The spiders now have bearings to offer a quieter operation of the pickup as well as giving the reel higher durability (longer life). Left, right, and center spider gears are all larger on the premium pickups for increased life.
The premium pickup offers the low-profile design that owners love while adding the durability of larger components needed for large baling operations. This pickup makes baling easier, especially in wide or windblown windrows, and increases productivity; more hay volume means more bales per hour.
- Flare-to-flare width of 1.8 m (71 in.) on balers with a 1.22-m (4-ft) wide bale chamber
- Flare-to-flare width of 2.2 m (86.6 in.) on balers with a 1.52-m (5-ft) wide bale chamber
- MegaWide Plus pickup makes it easier to produce better-shaped bales and improves crop pickup in wide, windblown, or scattered windrows
- Mega teeth, located at the ends of the pickup, pull crop around the flares when baling wide or windblown windrows
- Mega Tough™ pickup teeth provide greater strength and durability
- Exclusive square design handles high-impact loads without yielding
- Sturdy toothbar design
- Self-adjusting roller baffle
- Spiral rotor feed system improves feeding in all crop conditions
- Chain driven for positive feeding
- Cutout clutch protected
- Semi-pneumatic gauge wheels
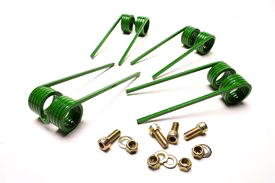

Mega and MegaTough pickup teeth are base equipment:
- Mega teeth, at the ends of the pickup, are heavy-duty for long life and improved crop retrieval
- Mega Tough pickup teeth are designed to withstand the harshest baling conditions and provide long service life
The 1.22-m (4-ft) balers use a reinforced, full-length toothbar design.
The 1.53 m (5-ft) balers use a heavy, C-channel construction. The pickup toothbars are divided into two half-sections that mount to a center spider for increased strength and even crop feeding.
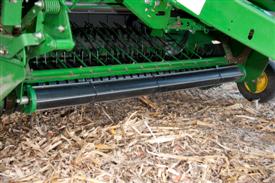

Available only on the MegaWide Plus pickup, the patented roller baffle is self-adjusting and produces smoother crop flow across the pickup. The roller also improves crop pick up in small windrows and prevents roll ahead of crop.
When combined with the MegaWide Plus pickup, this feeding system allows increased ground speed with less chance of plugging for increased productivity in all field conditions.
- Self-adjusting
- Smoothes crop for even flow across pickup
- Allows for faster ground speed with less chance of plugging
- Increases operator productivity
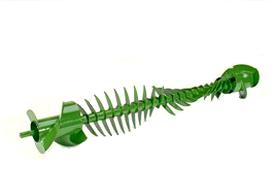
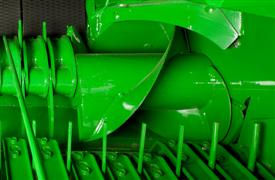
The MegaWide Plus pickup uses a rotor feeding assembly, which mounts behind the pickup for smooth and even crop flow into the bale chamber.
- Augers and rotor teeth are driven on the same shaft, eliminating the need for additional drives.
- The rotor is fixed to the baler frame, allowing positive and even feeding into the bale chamber.
- Large-diameter converging augers have high crop-flow capacity, and auger scrolls help to force crop into the chamber.
- Spiral design enhances feeding in uneven windrows and reduces loading on the rotor.
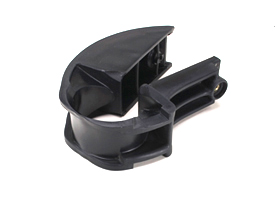

Rotor strippers allow crop to be lifted from the rotor teeth into the chamber without cutting or wrapping the crop.
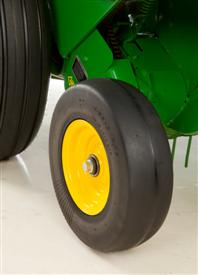

Semi-pneumatic gauge wheels provide smooth ground gauging over uneven terrain and protection to the pickup.
- Stiffer rubber sidewalls
- No air pressure to maintain, which mean no flat tires
- Adjustable to meet pickup tooth-to-stubble height requirements
The pickup float springs are positioned for excellent flotation.
- Adjustable to meet varying field conditions
- Float springs only support the pickup reel
- Rotor assembly is fixed to the baler frame, eliminating additional weight on the pickup system
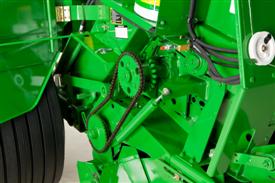

The MegaWide Plus pickups are chain-driven for positive bale starts with cutout clutch protection. The pickup is now being driven off the drive roll and bypasses the starter roll. This will allow for reduced wear and breakage of the starter roll chain.
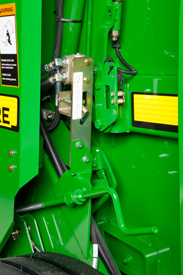

The adjusting crank positions the pickup to the desired operating height to match crop or field conditions.
An optional hydraulic pickup lift cylinder is available as an attachment.
- Makes raising for transport or clearing obstructions easy
- Crank handle serves as a down stop
- Adapts to regular, MegaTooth™ and MegaWide Plus pickups
- Hydraulic pickup lift comes standard on premium machines
Exclusive DiamondTough™ belts with plate-type splices
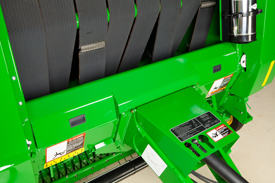

John Deere's 178 mm (7-in.) wide diamond-tread design ensures fast bale starts and grips the bale to prevent slippage and reduce chaffing. The treads are self-cleaning to reduce carryover.
The belts are staggered to reduce the loss of fine material and are closely spaced to contain the hay for fast, easy starts.
The belts enclose 91 percent of the bale width to reduce loss of fine material and retain hay quality.
The staggered belt roll design enables any loose hay under or behind the belts to be returned to the pickup and into the baler.
This design helps to prevent buildup at the front of the baler, which could cause hay loss and belt or splice damage.
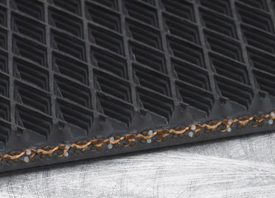

The 459, 459 Silage Special, 559, 559 Silage Special, 469, 469 Silage Special, 469 Premium, 569, 569 Silage Special, and 569 Premium use DiamondTough belts.
Belts are constructed using a patented triple-weave process of nylon and polyester materials.
They have the strength to handle heavy shock loads and help maintain consistent belt length.
The DiamondTough belts are more puncture and tear resistant than other belts on the market and provide improved belt life and reliability.
Plate-type fasteners
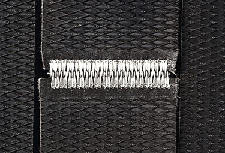

The 459, 459 Silage Special, 559, 559 Silage Special, 469, 469 Silage Special, 469 Premium, 569, 569 Silage Special, and 569 Premium use plate-type fasteners.
This closed-loop design uses a plate fastener with pre-assembled rivets that lock the fasteners into the belt, providing a powerful vice-type grip on the belt.
- The plates and rivets are manufactured from high-tensile stainless steel.
- Strong belt splices mean less maintenance and more productivity.
- The loop area is cold forged, making it extremely wear resistant in the coupling area, resulting in a very long cycle life.
- The spring steel pin is notched and locks into the splice connection without having to bend the pin or use external retainers.
The 9 Series Round Balers are driven by Diamond® Chain for superior performance
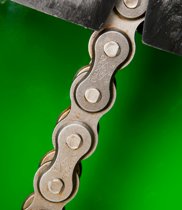
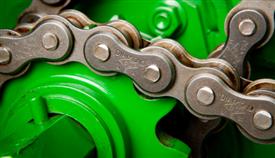
Diamond Chain's Diamond Series is an American-made product that is engineered, manufactured, and assembled in Indianapolis, Indiana since 1890. Diamond Chain’s unrivaled experience, unsurpassed quality, and unparalleled performance are the keys to building an industry-leading roller chain, because when it comes to performance, nothing outlasts a Diamond.
What gives Diamond Chain its superior chain performance?
Materials
Diamond Chain uses raw materials that meet exacting standards for metal grade, mechanical properties, carbon, and alloy content to ensure the minimization of impurities that impact tensile and fatigue strength.
These proprietary standards enable Diamond Chain components to maintain tighter tolerances throughout the fabrication and assembly process for a finished product with unparalleled quality, performance, and longevity.
Fabrication
While roller chain may appear to be a simple product, the number of components in a 3-m (10-ft) section of 40-pitch chain totals 1200 pieces - each a potential point of failure.
Diamond Chain designs each component to exacting dimensional standards and has a rigorous quality control system in place to ensure that only qualified pieces reach the final assembly stage.
- Plates: inner and outer plates go through a four-stage pitch-hole process. A multi-stage process is utilized to create a maximum bearing area that is straight, smooth, and burr free.
- Pins: precision grinding ensures consistent fit and smooth travel.
- Rollers: seamless roller design and dimensional control allows for extrusion with near-perfect roundness.
- Bushings: dimensional control enables bushings to be extruded with uniform wall thickness and concentricity for smooth travel. Near-perfect roundness increases the effective bearing area for the pin.
Heat treatment
The Diamond Chain company heat treats components using dedicated carburizing furnaces set to precise temperatures.
Through strict control of both atmosphere and quench, Diamond Chain components receive maximum carbon penetration for a high-carbon surface and low-carbon core. The process ensures consistent depth of case hardening increasing strength, durability, and wear resistance.
Shot peening
The Diamond Chain company uses proprietary shot-peening machinery developed and custom made to ensure consistent intensity and coverage of components during the shot peen process.
This highly controlled process ensures that components receive the same level of treatment for a consistent compressive surface stress that helps to increase fatigue resistance.
Lubrication
Diamond understands the importance of proper lubrication and its impact on a chain's wear life. Diamond Chain uses both proprietary lubrication formula and hot dip application process on all lubricated roller chains. The hot dip process ensures complete coverage of components while the proprietary lubricant maintains maximum continuing surface retention following the treatment. Special additives in the lubricant further enhance corrosion protection and extend wear life.
Preloading
The final stage of the manufacturing and assembly process for each Diamond roller chain is the preloading stage. Preloading approximates the recommended maximum loading during usage and is done to firmly seat pins and bushings in place and eliminate any initial elongation that may take place.
Diamond Chain comes standard on all 9 Series Round Balers.
The 449 Round Baler has 60 Diamond chain for its upper drive roll chain and 60H for its lower drive roll chain.
The 459E, 459, 459 Silage Special, 559, and 559 Silage Special have 60H Diamond Chains for their upper and lower drive roll chains.
The 469, 469 Silage Special, 569, and 569 Silage Special have 80 Diamond Chains for their upper and lower drive roll chains.
The 469 Premium and 569 Premium Round Balers have 80H Diamond Chain for their upper and lower drive roll chains.
Diamond is a trademark of Diamond Chain Company Inc. Please visit its website for more information.
Reduce fatigue with tractor-baler automation
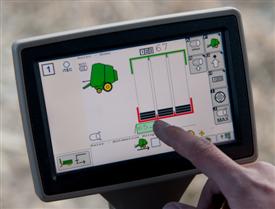

Tractor-baler automation allows for easier operation and reduced operator fatigue after all day operation. This function is only compatible with model year 2010 or newer John Deere 6030/7030 Premium, or model year 2011 or newer 6R/7R/8R Tractor that is GreenStar™- or AutoTrac™-ready.
6030 Premium Tractors include: 6230 Premium, 6330 Premium, and 6430 Premium Tractors.
7030 Premium Tractors include: 7130 Premium, 7230 Premium, 7330 Premium, 7430 Premium, and
7530 Premium Tractors.
All tractors must be ISOBUS compatible. All balers must have a pushbar when operating in tractor-baler automation mode.
NOTE: 6R Series Tractors can still be ordered non-ISO compatible. Please order the GreenStar-ready wiring harness package or AutoTrac-ready wiring harness package to make the 6R Tractor ISO compatible. Model year 2015 and newer Final Tier 4 6R Series Tractors must be ordered AutoTrac-ready from the factory in order to work with tractor-baler automation.
NOTE: Premium Round Balers can run on any tractor that is ISOBUS compatible (or made ISOBUS compatible with wiring harness) however, tractor-baler automation will only work on the tractors/features listed.
NOTE: Having the ISOBUS coupler does not necessarily mean that the tractor is GreenStar-ready.
There are two levels of tractor-baler automation. Both the baler activation and tractor activation must be purchased.
- Level 1: Selective control valve (SCV) control
- Requires electronic SCVs
- Controls the SCV for the gate. Tractor movement must be at zero before gate will open
- Operator must still start, stop, and drive the tractor.
- Operator must still weave if necessary.
- Level 2: SCV and vehicle speed control
- Requires electronic SCV’s and Infinitely Variable Transmission (IVT™) tractor
- Controls the SCV for the gate and the starting and stopping of the tractor
- Operator must drive the tractor
- Operator must weave if necessary
- Tractor will slow to a stop when bale reaches full size
- Operator must cycle reverse lever from forward to neutral and back to forward or
- Operator must press and hold brakes before tractor comes to complete stop
- Tractor will drive forward after reverse lever is cycled or operator releases brakes
Other premium features
Gull wing doors
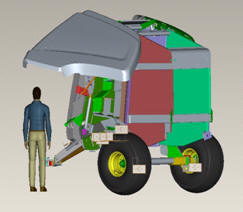
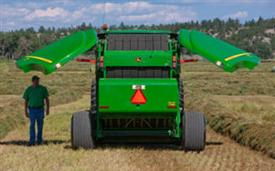
Gull wing doors are offered on the 469 Premium and 569 Premium Round Balers for differentiated styling. These doors allow the customer to easily service the machine. From the ground to the bottom of the door when open is 7 ft.
Factory-installed grease bank
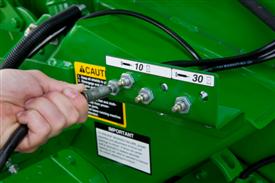

Standard on premium round balers is a factory-installed grease bank. This allows the customer to only have to grease eight zerks (four on each side of the baler) for grease zerks that were hard to reach on previous models. The customer will still have to grease the driveline and some other components on the baler.
Third bale shape sensor
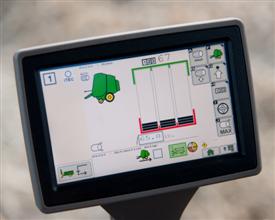

The 469 Premium and 569 Premium offer the customer a third bale shape sensor that can be turned on or off. This will allow the customer to make consistent, square shouldered bales since they can now see how the center of their bales are forming.
ISOBUS system
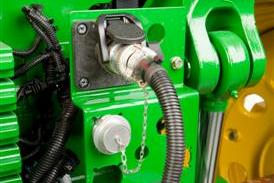
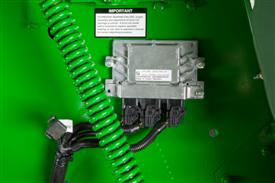
The ISOBUS system offered on the premium round balers allows the customer to use the latest technology when baling. They can utilize their GreenStar™ 2600, GreenStar 2630, GreenStar 1800, or certain R Series CommandCenter as their baling monitor and can switch between tractors without having to take the display with them. All information for the baler is stored on the controller.
Warranty
A new, two-year or 12,000-bale warranty comes standard on 469 Premium and 569 Premium Round Balers ONLY. Please see full product warranty for more details.
Related Products
-
348 Small Square Baler
-
450M Round Baler
-
460M Round Baler
-
460R Premium Round Baler
-
560M Round Baler
-
560R Premium Round Baler
-
A420R Accumulator
-
A520R Accumulator
-
C441R Wrapping Chamber Baler
-
C451R Variable Chamber Wrapping Baler
-
F441M Round Baler
-
F441R Round Baler
-
L331 Large Square Baler
-
L341 Large Square Baler
-
V451G Variable Chamber Baler
-
V451M Variable Chamber Baler
-
V451R Variable Chamber Baler
-
V461M Variable Chamber Baler
-
V461R Variable Chamber Baler