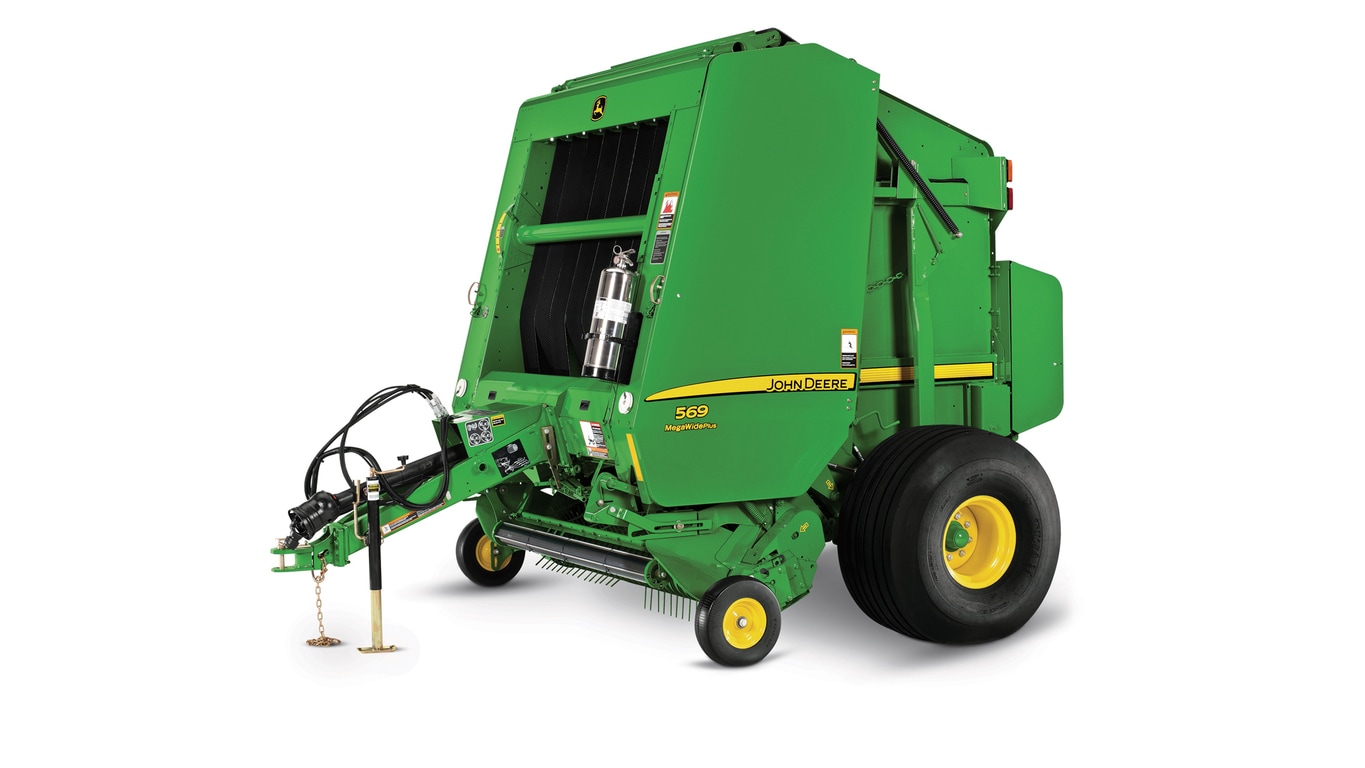
569
Round Baler
- BaleTrak™ Pro monitor-controller
- Adjustable hitch to match wide array of tractor drawbar heights
- MegaTooth™ pickup offers extra toughness in a regular pickup width
- Exclusive DiamondTough™ belts with plate-type splices
Features
BaleTrak™ Pro monitor-controller
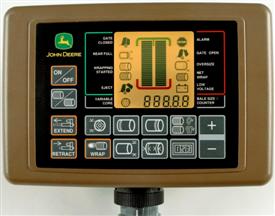

The 459, 459E, 459 Silage Special, 559, 559 Silage Special, 469, 469 Silage Special, 569, and 569 Silage Special Round Balers feature the BaleTrak Pro monitor-controller.
The 449 Round Baler offers the option to have the BaleTrak Pro monitor-controller. On the 449 and 459E this monitor does not allow for all the features of the BaleTrak Pro monitor such as bale shape bars and net wrap. Wrap settings and bale size can be viewed from the monitor.
This feature allows the operator to both monitor and control important baler functions for productivity and convenience right from the tractor seat.
A 24-bar graph makes it even easier to make a uniform-shaped bale that will stand tall and remain firm over time. The 24 bars provide smaller increments of change to give the operator a more precise indication of bale shape. The 449 and 459E Round Balers do not utilize the bale shape bars like the other models do.
Preset factory settings allow the operator to turn on just one switch and go bale; it's just that easy.
BaleTrak Pro provides the following monitoring functions:
- On/off key - turns monitor on or off
- Twine/net key - selects between twine or net wrap
- Baler symbol - gate closed, ready to bale
- 24-bar graph - bale-shape indicators
- Small bale symbol - near-full bale
- Bale with twine/net wrap symbol - stop forward travel, wrapping started, maintain power take-off (PTO) speed
- Baler with bale ejecting symbol - open gate and eject bale
- Numerical display - shows bale diameter increasing in inches
- Variable core symbol - on, if selected (variable core kit optional)
- Battery symbol - low-voltage indication
- Stop sign symbol alarm - stop baling immediately, investigate/correct
- Bale with net wrap symbol - net wrap did not feed or knife did not cut material
- Baler with gate open symbol - gate open, ejecting bale
- Numerical display - bale counter, daily/lifetime totals
- Error code display - displays the error code number for diagnosing the electrical system
- Slip clutch alert kit (optional)
BaleTrak Pro provides the following controlling functions:
- Set bale size
- Set twine spacing/net wrap
- Set the number of twine end wraps
- Manually extend twine arms
- Manually retract twine arms
- Adjust starting time of net wrap application
- Set the number of net wraps
- Set the distance of twine from bale ends
- Manual twine actuator movement with electronic bypass
- Onboard diagnostics
Features of BaleTrak Pro monitor-controller:
- Simple to operate; just turn on and bale
- Factory settings are preprogrammed but can be changed by the operator, if desired
- Added flexibility; the operator can adjust the baler for different crop conditions
- Increases productivity; the operator stays on the tractor
- Single self-contained processor box mounts on the tractor
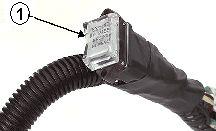
BaleTrak Pro has a manual twine arm override switch (1), which is included with the monitor's wiring:
- Allows operator to manually wrap twine on bale if BaleTrak Pro monitor-controller malfunctions
- Connects to tractor three-terminal convenience outlet
Adjustable hitch to match wide array of tractor drawbar heights
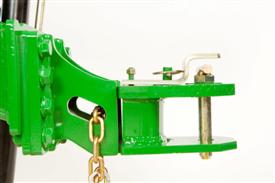
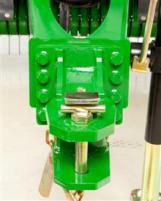
The 9 Series Round Balers come standard with an adjustable hitch. This feature allows the hitch height to be adjusted to optimize crop-feeding performance. Due to the wide array of tractor tire sizes and drawbar heights, hitch adjustment may be necessary to get the proper feed opening of the baler. The adjustable hitch eliminates the need for the 51-mm (2-in.) thick tractor drawbar kit (AE57344) because it has a wider opening.
Benefits of the adjustable hitch:
- Ability to match baler to numerous tire sizes
- Allows for drawbar height to fall within 330 mm to 559 mm (13 in. to 22 in.) from top of drawbar to the ground
- Eliminates narrow feed opening on baler which can cause plugging
- Allows pickup head to follow terrain without missing crop
All eight bolts must be used when adjusting the hitch. There are four different positions as shown below:
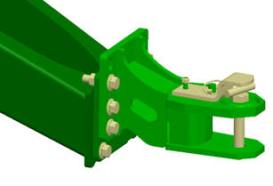
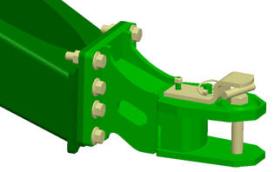
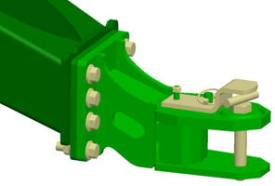
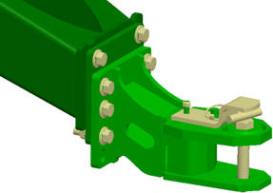
Also standard on all 9 Series Round Balers except the 459E is the drawbar flap. This helps to eliminate hay from getting caught on the hitch of the baler. The drawbar flap is designed to allow the operator to remove or attach the flap without having to unhook the baler from the tractor.
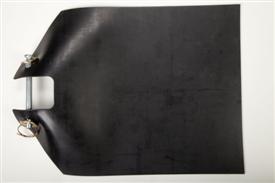
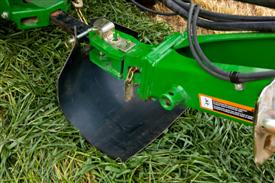
Regular pickup offers large feed opening and low-profile, mid-mounted pickup
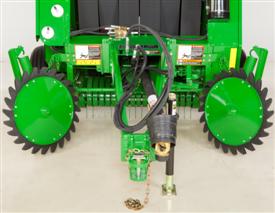

Mounted in front of the baler wheels and directly below the bale chamber, the pickup hugs the ground for clean crop retrieval. Hay movement is minimized.
- V-belt driven
- 449, 459E, and 459 Baler pickups are 116.6 cm (45.9 in.) wide
- 559 and 569 Baler pickups are 156 cm (61.4 in.) wide
- Large reel shaft and reel bearing
The small-diameter, low-profile pickup allows for good ground gauging and clean crop retrieval.
- Handles large, heavy windrows of hay and high-moisture crops
- Feeds hay directly to the forming chamber to reduce crop loss
- Low-profile pickup minimizes hay lift to reduce chaffing to retain hay quality
Side flares prevent hay from blowing off the pickup ends and reduce hay loss.
The closely spaced pickup teeth extend to the baler side sheets to help build straight-edged bales.
Standard on regular and MegaTooth™ pickups, compressor rods are contoured to control hay over the pickup radius for positive feeding. The compressor rack can be adjusted upward or downward to match the volume of material in windrow and can be easily removed to match crop conditions.
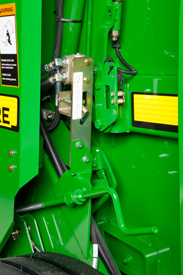

The adjusting crank positions the pickup to the desired operating height to match crop or field conditions.
An optional hydraulic pickup lift cylinder is available as an attachment.
- Makes raising for transport or clearing obstructions easy
- Crank handle serves as a down stop
- Adapts to regular, MegaTooth and MegaWide™ Plus pickups
- Hydraulic pickup lift comes standard on premium machines
MegaTooth™ pickup offers extra toughness in a regular pickup width
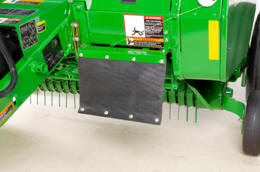
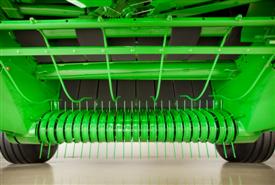
Available on the 569 Baler only, John Deere exclusive, patented MegaTooth pickup is the same width as the bale chamber, but includes these heavy-duty components as standard equipment:
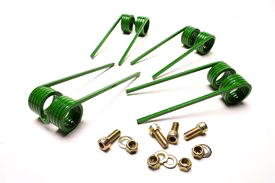

- Mega teeth, located at the ends of the pickup, pull crop around the flares
- MegaTough™ pickup teeth provide greater strength and durability
- Exclusive square design handles high-impact loads without yielding


The balers are chain-driven for positive bale starts with cutout clutch protection. The pickup is now being driven off the right-hand side of the baler and bypasses the starter roll chain. This will allow for reduced wear on the starter roll chain.
Other features of the pickup include:
- Chain drive for positive bale starts
- Cutout clutch protected
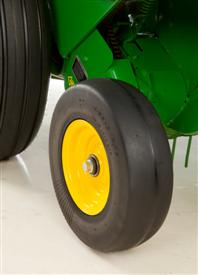

Semi-pneumatic gauge wheels are standard on the MegaTooth pickup and provide smooth ground gauging over uneven terrain:
- Stiff rubber sidewalls
- No air pressure to maintain, which means no flat tires
- Adjustable to meet pickup tooth-to-stubble height requirements
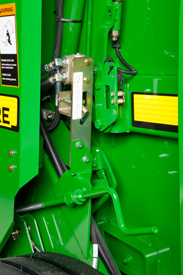

The adjusting crank positions the pickup to the desired operating height to match crop or field conditions.
An optional hydraulic pickup lift cylinder is available as an attachment.
- Makes raising for transport or clearing obstructions easy
- Crank handle serves as a down stop
- Adapts to regular, MegaTooth and MegaWide™ Plus pickups
- Hydraulic pickup lift comes standard on premium machines
MegaWide™ Plus pickup with MegaTough™ pickup teeth offers super capacity
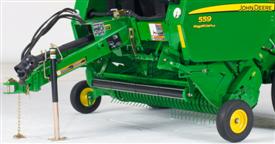

A MegaWide Plus pickup is available on 449, 459, 559, and 569 Round Balers. It is base equipment on the 459 Silage Special, 559 Silage Special, 469, 469 Silage Special, and 569 Silage Special Balers.
This pickup makes baling easier, especially in wide or windblown windrows, and increases productivity; more hay volume means more bales per hour.
- Flare-to-flare width of 1.8 m (5.9 ft) on balers with a 1.2 m (4-ft) wide bale chamber
- Flare-to-flare width of 2.2 m (7.2 ft) on balers with a 1.5-m (5-ft) wide bale chamber
- MegaWide Plus pickup makes it easier to produce better-shaped bales and improves crop pickup in wide, windblown, or scattered windrows
- Mega teeth, located at the ends of the pickup, pull crop around the flares when baling wide or windblown windrows
- MegaTough pickup teeth provide greater strength and durability
- Exclusive square design handles high-impact loads without yielding
- Sturdy toothbar design
- Self-adjusting roller baffle
- Spiral rotor-feed system improves feeding in all crop conditions
- Chain driven for positive feeding
- Cutout clutch protected
- Semi-pneumatic gauge wheels
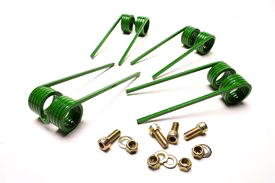

Mega and MegaTough pickup teeth are base equipment:
- Mega teeth, at the ends of the pickup, are heavy-duty for long life and improved crop retrieval
- MegaTough pickup teeth are designed to withstand the harshest baling conditions and provide long service life
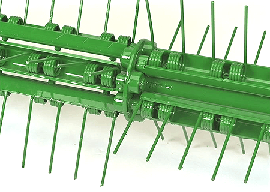

The 1.2-m (4-ft) balers use a full-length, reinforced toothbar design.
The 1.5-m (5-ft) balers use a heavy, C-channel construction. The pickup toothbars are divided into two half-sections that mount to a center spider for increased strength and even crop feeding.
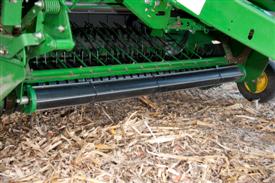

Available only on the MegaWide Plus pickup, the patented roller baffle is self-adjusting and produces smoother crop flow across the pickup. The roller also improves crop pickup in small windrows and prevents roll ahead of crop.
When combined with the MegaWide Plus pickup, this feeding system allows increased ground speed with less chance of plugging, for increased productivity in all field conditions.
- Self-adjusting
- Smoothes crop for even flow across pickup
- Allows for faster ground speed with less chance of plugging
- Increases operator productivity
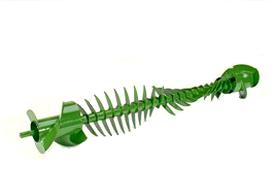
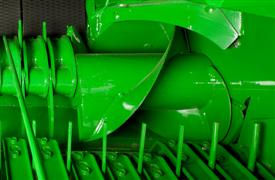
The MegaWide Plus pickup uses a rotor feeding assembly, which mounts behind the pickup for smooth and even crop flow into the bale chamber.
- Augers and rotor teeth are driven on the same shaft, eliminating the need for additional drives.
- The rotor is fixed to the baler frame, allowing positive and even feeding into the bale chamber.
- Large-diameter converging augers have high crop-flow capacity, and auger scrolls help to force crop into the chamber.
- Spiral design enhances feeding in uneven windrows and reduces loading on the rotor.
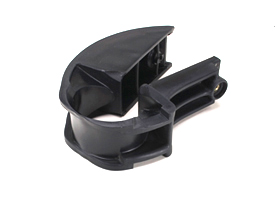

Rotor strippers allow crop to be lifted from the rotor teeth into the chamber without cutting or wrapping the crop.
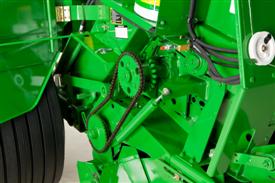

The MegaWide Plus pickups are chain-driven for positive bale starts with cutout clutch protection. The pickup is now being driven off the drive roll and bypasses the starter roll. This will allow for reduced wear and breakage of the starter roll chain.
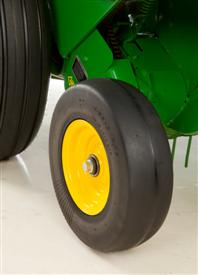

Semi-pneumatic gauge wheels provide smooth ground gauging over uneven terrain and protection to the pickup.
- Stiffer rubber sidewalls
- No air pressure to maintain, which mean no flat tires
- Adjustable to meet pickup tooth-to-stubble height requirements
The pickup float springs are positioned for excellent flotation.
- Adjustable to meet varying field conditions
- Float springs only support the pickup reel
- Rotor assembly is fixed to the baler frame, eliminating additional weight on the pickup system
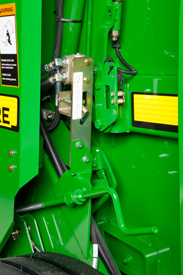

The adjusting crank positions the pickup to the desired operating height to match crop or field conditions.
An optional hydraulic pickup lift cylinder is available as an attachment.
- Makes raising for transport or clearing obstructions easy
- Crank handle serves as a down stop
- Adapts to regular, MegaTooth and MegaWide™ Plus pickups
- Hydraulic pickup lift comes standard on premium machines
Vertical forming chamber maintains uniform bale density
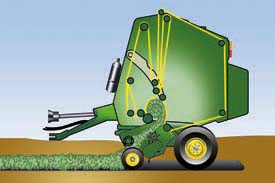

As the hay enters the forming chamber from the pickup, belts turn the hay immediately to form a tight, dense core.
Incoming hay then feeds between the bale and the lower-gate roll. Hay is tightly compressed into smooth, dense layers as it enters the bale.
Chaffing is greatly reduced to prevent loss and retain hay quality in the bale.
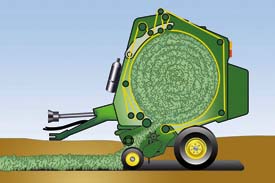

The idler arm rises with bale growth, forcing oil from the hydraulic cylinder through a pressure-relief valve:
- Maintains uniform bale density throughout the bale-forming process
Exclusive DiamondTough™ belts with plate-type splices
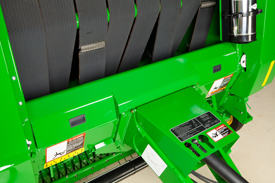

John Deere's 178 mm (7-in.) wide diamond-tread design ensures fast bale starts and grips the bale to prevent slippage and reduce chaffing. The treads are self-cleaning to reduce carryover.
The belts are staggered to reduce the loss of fine material and are closely spaced to contain the hay for fast, easy starts.
The belts enclose 91 percent of the bale width to reduce loss of fine material and retain hay quality.
The staggered belt roll design enables any loose hay under or behind the belts to be returned to the pickup and into the baler.
This design helps to prevent buildup at the front of the baler, which could cause hay loss and belt or splice damage.
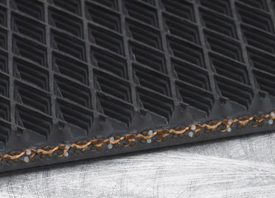

The 459, 459 Silage Special, 559, 559 Silage Special, 469, 469 Silage Special, 469 Premium, 569, 569 Silage Special, and 569 Premium use DiamondTough belts.
Belts are constructed using a patented triple-weave process of nylon and polyester materials.
They have the strength to handle heavy shock loads and help maintain consistent belt length.
The DiamondTough belts are more puncture and tear resistant than other belts on the market and provide improved belt life and reliability.
Plate-type fasteners
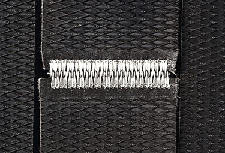

The 459, 459 Silage Special, 559, 559 Silage Special, 469, 469 Silage Special, 469 Premium, 569, 569 Silage Special, and 569 Premium use plate-type fasteners.
This closed-loop design uses a plate fastener with pre-assembled rivets that lock the fasteners into the belt, providing a powerful vice-type grip on the belt.
- The plates and rivets are manufactured from high-tensile stainless steel.
- Strong belt splices mean less maintenance and more productivity.
- The loop area is cold forged, making it extremely wear resistant in the coupling area, resulting in a very long cycle life.
- The spring steel pin is notched and locks into the splice connection without having to bend the pin or use external retainers.
The 9 Series Round Balers are driven by Diamond® Chain for superior performance
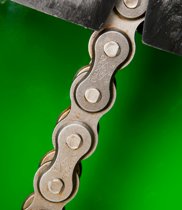
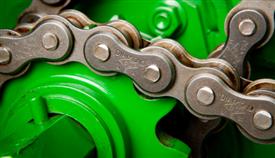
Diamond Chain's Diamond Series is an American-made product that is engineered, manufactured, and assembled in Indianapolis, Indiana since 1890. Diamond Chain’s unrivaled experience, unsurpassed quality, and unparalleled performance are the keys to building an industry-leading roller chain, because when it comes to performance, nothing outlasts a Diamond.
What gives Diamond Chain its superior chain performance?
Materials
Diamond Chain uses raw materials that meet exacting standards for metal grade, mechanical properties, carbon, and alloy content to ensure the minimization of impurities that impact tensile and fatigue strength.
These proprietary standards enable Diamond Chain components to maintain tighter tolerances throughout the fabrication and assembly process for a finished product with unparalleled quality, performance, and longevity.
Fabrication
While roller chain may appear to be a simple product, the number of components in a 3-m (10-ft) section of 40-pitch chain totals 1200 pieces - each a potential point of failure.
Diamond Chain designs each component to exacting dimensional standards and has a rigorous quality control system in place to ensure that only qualified pieces reach the final assembly stage.
- Plates: inner and outer plates go through a four-stage pitch-hole process. A multi-stage process is utilized to create a maximum bearing area that is straight, smooth, and burr free.
- Pins: precision grinding ensures consistent fit and smooth travel.
- Rollers: seamless roller design and dimensional control allows for extrusion with near-perfect roundness.
- Bushings: dimensional control enables bushings to be extruded with uniform wall thickness and concentricity for smooth travel. Near-perfect roundness increases the effective bearing area for the pin.
Heat treatment
The Diamond Chain company heat treats components using dedicated carburizing furnaces set to precise temperatures.
Through strict control of both atmosphere and quench, Diamond Chain components receive maximum carbon penetration for a high-carbon surface and low-carbon core. The process ensures consistent depth of case hardening increasing strength, durability, and wear resistance.
Shot peening
The Diamond Chain company uses proprietary shot-peening machinery developed and custom made to ensure consistent intensity and coverage of components during the shot peen process.
This highly controlled process ensures that components receive the same level of treatment for a consistent compressive surface stress that helps to increase fatigue resistance.
Lubrication
Diamond understands the importance of proper lubrication and its impact on a chain's wear life. Diamond Chain uses both proprietary lubrication formula and hot dip application process on all lubricated roller chains. The hot dip process ensures complete coverage of components while the proprietary lubricant maintains maximum continuing surface retention following the treatment. Special additives in the lubricant further enhance corrosion protection and extend wear life.
Preloading
The final stage of the manufacturing and assembly process for each Diamond roller chain is the preloading stage. Preloading approximates the recommended maximum loading during usage and is done to firmly seat pins and bushings in place and eliminate any initial elongation that may take place.
Diamond Chain comes standard on all 9 Series Round Balers.
The 449 Round Baler has 60 Diamond chain for its upper drive roll chain and 60H for its lower drive roll chain.
The 459E, 459, 459 Silage Special, 559, and 559 Silage Special have 60H Diamond Chains for their upper and lower drive roll chains.
The 469, 469 Silage Special, 569, and 569 Silage Special have 80 Diamond Chains for their upper and lower drive roll chains.
The 469 Premium and 569 Premium Round Balers have 80H Diamond Chain for their upper and lower drive roll chains.
Diamond is a trademark of Diamond Chain Company Inc. Please visit its website for more information.
XL high-flotation tires
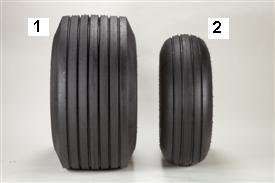
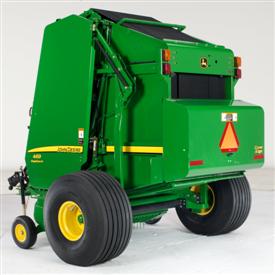
The XL high-flotation 21.5L-16.1 10 PR tires (1) are available on 459, 459 Silage Special, 559, 559 Silage Special, 469, 469 Silage Special, 469 Premium, 569, 569 Silage Special, and 569 Premium. All machines must have MegaWide™ Plus pickup.
The high-flotation 14L–16.1 tires (2) are available on all models except the 459E, 469 Premium, 569 Silage Special, and 569 Premium. The 14L – 16.1 tires have replaced the 31 x 13.5 tires.
The larger tires absorb shock loads and improve the ride in rough or pivot track ground, decreases compaction in soft ground, and allows increased ground speed for increased productivity.
Related Products
-
348 Small Square Baler
-
450M Round Baler
-
460M Round Baler
-
460R Premium Round Baler
-
560M Round Baler
-
560R Premium Round Baler
-
A420R Accumulator
-
A520R Accumulator
-
C441R Wrapping Chamber Baler
-
C451R Variable Chamber Wrapping Baler
-
F441M Round Baler
-
F441R Round Baler
-
L331 Large Square Baler
-
L341 Large Square Baler
-
V451G Variable Chamber Baler
-
V451M Variable Chamber Baler
-
V451R Variable Chamber Baler
-
V461M Variable Chamber Baler
-
V461R Variable Chamber Baler